Sugatsune introduces Swivel Torque Hinge HG-S for smooth…
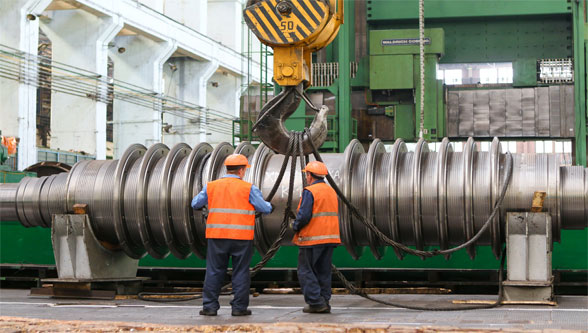
Key trends in predictive maintenance | ENGINEERING REVIEW |Manufacturing | Industrial Sector Magazine & Portal
According to Deloitte, unplanned downtime is costing industrial manufacturers USD 50 billion each year. This figure is alarming but by no means a surprise to industry experts. Here, John Young, APAC sales director for automation parts supplier, EU Automation, discusses the benefits of predictive maintenance (PdM) in the manufacturing industry and three trends to watch out for.
PdM is designed to help manufacturers establish the condition of their machinery and accurately predict when maintenance is needed. This can minimize costly downtime due to equipment failure and reduce maintenance costs.
However, the real-time data captured from sensors can not only minimize the risk of unplanned downtime but can actually increase production performance and operational efficiency. This has clear benefits for industrial businesses. For example, manufacturers can increase their equipment lifespan, reduce energy and resource consumption, as well as minimize health and safety concerns. As with many other maintenance strategies, PdM is evolving, and here are three trends to watch out for.
Thermography techniques
Heat can be an early indicator of equipment damage or malfunction. Thermographic analysis is a non-destructive testing technique, that uses infrared scanners to detect wear and rusting of equipment that would normally go unnoticed to the naked eye.
Manufacturers who conduct regular infrared PdM checks on the temperature of their equipment will save money on reactive maintenance fees and equipment repair costs. Moreover, manufacturers can manage their equipment lifecycles by monitoring the condition over time and identifying unusual readings that require further inspection. As a result, they will catch potential failures and avoid unplanned downtime.
The latest thermography techniques include thermal imaging. A thermal imager is a non-contact technology that helps manufacturers detect problems at a safe distance during inspections. It takes infrared temperature measurements and converts the information into an image. This application allows manufacturers to measure and compare the temperatures for each piece of equipment, without disrupting production.
Plug and play technology
Many manufacturers depend on legacy equipment to run important application processes. However, the machines are not equipped with connectivity to send real-time data. Plug and play (PnP) devices allow manufacturers to connect legacy machines without going through expensive machinery replacements.
PnP devices can be used by manufacturers in a range of production tasks across a facility and are designed to work straight out of the box. They do not require installation fees, or specific skills to get started. The MICA IIoT from Bosch and Harting can be installed to any machine to improve condition monitoring and alert maintenance engineers of potential problems.
Predictive maintenance as a service
Another upcoming trend is PdM as a service, especially for original equipment manufacturers (OEM). PdM changes the way OEMs deliver their service by allowing them to collect real-time performance data from their customer’s equipment.
This gives them a unique advantage when it comes to predictive analytics, as OEMs can build models from the data collected from their customer base and provide individual insights and equipment specific maintenance targets. PdM as a service delivers value from day one, detecting early warning signs of equipment failure, and scheduling maintenance.
PdM technologies are improving all the time, as more and more factories exploit the benefits of greater connectivity. By harnessing the latest technology to supplement PdM strategies, manufacturers can save costs, optimize equipment performance, and reduce the risk of unplanned downtime.
EU Automation is a global supplier of industrial equipment. If you are looking to source automation parts for your machinery and equipment, visit the EU Automation website to view the full product range.