Solar Land-based EPC Solutions: Pioneering the Future of…
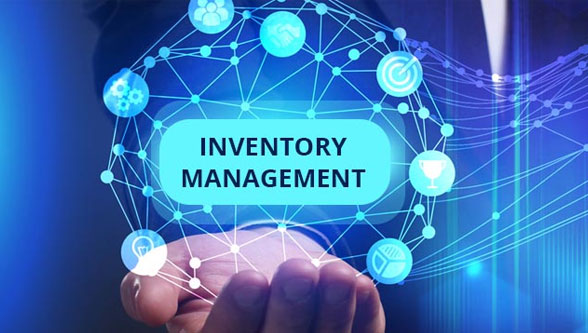
Inventory Management – strategic perspective for uncertain pandemic times
Quality rejections, rework, machine maintenance issues, poor production planning, manpower related issues, etc. are some of the inefficiencies most of the processes would carry, and will drain the organisational resource and render it non-competitive
Every manufacturing unit (of all scale & type) across necessarily works on three major resources: Man, Machine and Material.
Most of the industrial engineering concepts, Lean manufacturing principles and operational excellence programs have always focussed to run the operations with least of these resources (Man, Machine and Material). Journey of operational excellence can be summarised in simple words as “How to produce more with lowest of these vital resources”.
Man, and Machine are mostly fixed resources and do not offer flexibility to vary at tactical or operational level. Mostly what gets budgeted and implemented as part of the strategy of the organisation, holds good, unless there is strategic rethink to alter the resources.
However, Material as a resource is most volatile of all. More often than not, there is a tendency to creep beyond minimum inventory to be maintained. Since the material would be used if not today, at least soon, has a tendency to slip out of the radar of clinical review.
Higher Inventory Masks Process inefficiencies
Quality rejections, rework, machine maintenance issues, poor production planning, manpower related issues, etc. are some of the inefficiencies most of the processes would carry. They are inherently available in all the processes – only the degree may vary based on the maturity of the organisation.
All these inefficiencies will drain the organisational resource and render it non-competitive in the long run. So, it is critical that these inefficiencies surface up and get adequate focus so that they are addressed.
While the intention of an organisation would be to alleviate these inefficiencies, higher level of inventory would mask them. Any quality rejections would be supplemented by another material in stock; any delay due to machine breakdown issues would get compensated by semi-finished stock available in system.
So, even though higher inventory would help in operations running, it would make the organisation less competent in the long run.
Impact of Inventory on Financials
Over and above its impact on process efficiency, higher inventory will also have serious impact on the Working Capital. It is always desirable to have high velocity in the process, wherein input (raw material) is converted to output (finished good) at fastest possible speed. But longer the time it takes for this conversion or larger the material in system, cash flow cycle gets stretched. Especially in sectors where companies are relying on external finances for working capital need, even a marginal increase in system inventory would have significant ramification.
World Class Manufacturing (WCM) and Lean on Inventory
Both World Class Manufacturing literature and Lean has clear prescription on inventory management. Based on the voices of many Lean veterans + based on a plethora of literature available in public domain, following inferences can be drawn as recommendation on inventory:
Raw material (RM) Inventory:
- Maintain raw material inventory sufficient to address the variance in supply input
- Have continuous effort to stabilise the supply variance
- Have time bound effort to convert all supplies to ‘Just in Time (JIT)’ delivery from the supplies
Semi-finished (SF) inventory:
Maintain semi-finished inventory as a tactical short-term measure to address production variance
Initiate continuous drive to stabilise production variances
- Aim for ‘0’ semi-finished inventory. Any production work started on a raw material should continuously progress till FG without getting stocked up @ any stage
Finished Goods (FG) Inventory
Maintain FG only to the extent required to meet demand fluctuation. Otherwise, postpone the start of production to have lowest slack (buffer) in the FG stage. Target to ship it to customer once the production process is complete.
Ideal case In some of the Toyota plants, finished good is directly loaded on to ship from the factory for dispatch
Summary: In a nutshell, produce what is required in the right quantity at the right time so that there is completely no slack in inventory. This would be an ideal Lean manufacturing facility.
Concurrent Inventory Management practices in Indian Manufacturing Industry
Due to considerable influence of Japanese firms on Indian manufacturers, there has been an appreciable effort in almost all the sectors in making their processes Lean. There is almost complete unanimity among Indian manufacturers that Lean helps to make the process better and make them globally competitive. There has been significant effort to cut down the inventory and to increase the velocity of manufacturing cycle (throughput).
However, the success of this endeavour has not been uniform across the industry. While some of the sectors/ companies have been able to make significant strides in making their operations lean, there are many who have not been so successful due to their own operational constraints. Geographical and logistical factors which are specific to India have also played a significant influencing role on Inventory management.
Impact of Pandemic on Inventory Management Process
Due to repeated lockdowns, volatility in workforce availability, prevalent apprehensions in the factories, the supply chain has become nervous. Even after seven months of being in pandemic situation, there is no definite end of sight about how long this uncertainty will last. There is no clarity on nature of challenges which would unfold in the days to come.
However, to keep the business running and ensure there are minimal shocks on the supply chain, there is a need of strategic rethink on Inventory management of an organisation.
The earlier hypothesis of lesser inventory, Just in Time production/ supplies needs to be relooked. Strategically, we need to redesign the inventory management practice based on supplier performance, demand fluctuations and other operational constraints. The section below tries to highlight the approach specific to pandemic time.
Framework for Inventory Profiling in Pandemic times
The framework below gives a road map at a high level. Based on industry specific requirements and organisation constraints, the framework needs to be suitably modified for more effectiveness.
Raw Material Inventory
If answer to any of the questions in text box below is “YES”, then you may need to stock up the inventory in RM Stage till supply chain disruptions (caused by pandemic) are completely resolved.
Semi-Finished (SF) Inventory
If answer to any of the questions in text box below is “YES”, then you may need to stock up the inventory in SF Stage till supply chain disruptions (caused by pandemic) are completely resolved.
Finished Goods (FG) Inventory
If answer to any of the questions in text box below is “YES”, then you may need to stock up the inventory in FG Stage till supply chain disruptions (caused by pandemic) are completely resolved.
Conclusion:
The author of this article is a firm believer in Lean philosophy (and consequential minimal inventory). So, all recommendations mentioned in this article are only for Pandemic situation (when there is widespread supply chain disruption). It must be reviewed again and reversed for Lean Supply Chain and Lean Inventory once supply chain normalises.
Article by –
Adarsh Ramaswamy is Director at Sambuddha Management Consulting Pvt. Ltd.
ENGINEERING REVIEW provides cognitive exchange of information on the manufacturing sector, which will facilitate you keep updated on a real time basis.
Please follow our magazine page and also join our LinkedIn Group- exclusive group created for manufacturing professionals community
Join us on LinkedIn Group : https://www.linkedin.com/groups/10477764/
Follow us on LinkedIn : https://www.linkedin.com/company/engineering-review/