Sugatsune introduces Swivel Torque Hinge HG-S for smooth…
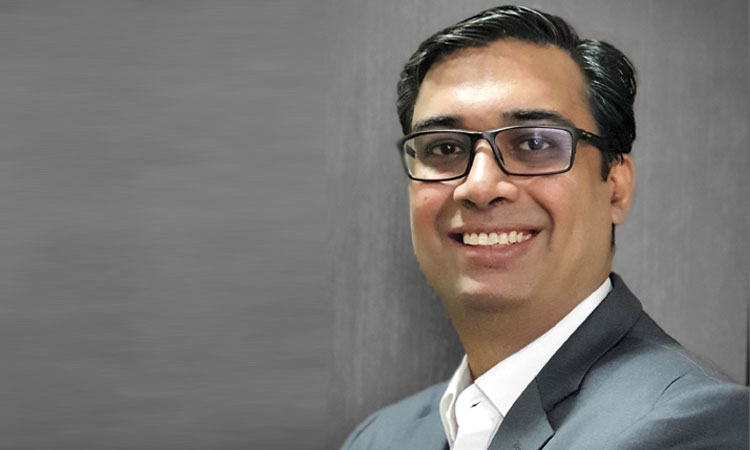
Industry For Welding Equipment | ENGINEERING REVIEW |Manufacturing | Industrial Sector Magazine & Portal
In modular technology, even if something goes wrong in one part of the machine, your overall machine doesn’t stop. One can still operate with the machine with lower ampere capacity. This is a path-breaking and a very innovative solution. Because earlier if there was any problem in the equipment, no matter what, the entire equipment would have stopped,” states Nimesh.
Manufacturing has emerged as one of the high growth sectors in India. Recently it was published that India has seen surge in the output of the natural gas, petroleum refinery production, fertilisers, steel, cement, and electricity. All these surge impact directly to manufacturing sectors including shipbuilding, automotive, offshore exploration, aerospace, oil & gas, energy, and construction where welding machine been used continuously and driving the welding machinery market today. With the implementation of multiple technology such as remote control and AI based robotic welding machine, it is bringing the needed revolution in the welding machinery industry. With the help of Make in India drive, India is on the path of becoming hub for global manufacturing giant. Clients are focusing more on the quality, reliability and cost effective products and expecting the same from their manufacturers. Mostly, clients end up having to choose what is available to suit their requirements.
Electronics Devices Worldwide Pvt Ltd has been established since 1974 making products in India for Global Use. With a well-established R&D department and proven product range we have exports in about 90 countries. SigmaWeld, brand was established in the year 2007, the company has been providing a complete Welding Solutions. The company has been parallel with the changing situation and successfully meeting the expectations of its clients in the Indian metalworking industry.
“We have a full-fledged R&D team, micro controller programmers, circuit designers, and application engineers. They are in-tuned and continuously working together to bring innovative products by integrating the latest technology. We see what can be done, and how can we add more value to the customer by giving life to innovative ideas. This helps us to be updated and stay ahead in the market. It also helps us customize solutions as per the expectation of our customers,” says Nimesh Chinoy, Marketing Director at SigmaWeld. “Another point is that we have our own sales and service team PAN India Offering a Complete Range of Innovative Welding Equipment SigmaWeld product offering includes Welding Inverters for ARC, TIG, MIG, SAW Welding applications, Value Added Products like Cold Wire Feeder, Hot Wire Tig Welding solutions, Data Monitoring system and Pre Weld Post Weld Induction heating, Welding SPMs, HardFacing and cladding solutions. Furthermore, SigmaWeld have developed and introduced smart welding series called SigmaWeld PRO Series for MIG, TIG & ACDC TIG Welding Inverters which are 100 percent duty cycle machines and comes with modular technology; an amalgamation of smaller modules which are specially programmed to offer advanced High End Welding solutions. Offering Flexibility with Enhanced deposition efficiency TIG welding typically is one of the best processes in the world, but is inherently slow. And because it is slow, it is also deemed as expensive. To overcome this SigmaWeld has developed SigmaWeld Accelerated TIG (SWAT) which works on Keyhole Technology. This technology is as such that the time cycle for operations will be reduced by 1/10th. This product is doing extremely well for the company’s clients who are welding difficult materials such titanium, nickel alloys, stainless steel, to name a few. Furthermore, the company’s SigmaTherm – Induction Heating Equipments also comprises pre-weld / post-weld induction heaters. This induction heater has an upright advantage over other heating processes as it does not create any flame, has a shorter time period, and most importantly saves oxygen, especially in these times. Moreover, the operator doesn’t get any heat, and hence would be more comfortable and productive.
Website: www.sigmaweld.com, www.electronicsdevices.com