Leading Industry Associations Unite to Support Auto Components…
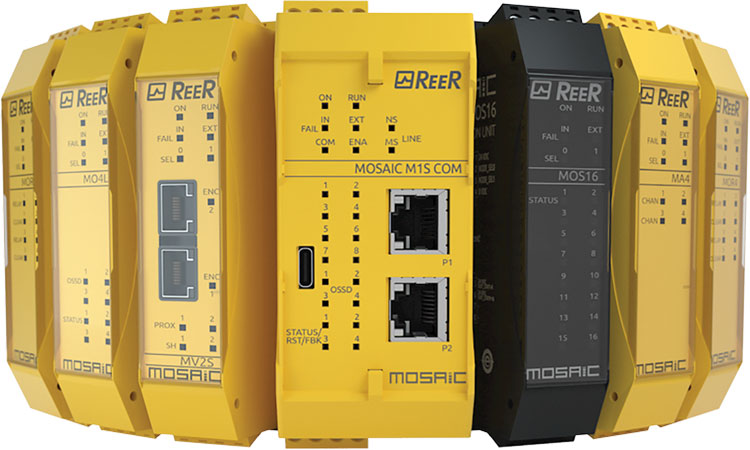
Industrial Thermal Processes | ENGINEERING REVIEW | Manufacturing | Industrial Sector Magazine & Portal | Indian Industrial Information | Manufacturing Industry Update | Manufacturing Technology Update
Example: ovens, dryers for ceramic or cereals, shrink-sleeve wrappers & spreading lines, etc…
Request
The most common requests for this kind of applications are the following:
- Flame monitoring, according to 13849-1 standard, must reach PL e safety level.
- Gas and burning oil pressure control (PL d).
- Post-purge monitoring of gas presence in pipes (PL d).
- Combustive-air ventilation turn-off control (PL d).
Note: With regards to these types of applications, a key factor should be highlighted: there should be no confusion between the actual “burner” and the plant or thermal process in which the burner is used. Burners must comply with specific standards requiring analogic reading functions of air-gas mixture and many other relating logic functions. Instead, standard EN 746-2 regulates burner’s applications defining the thermal process required safety levels and regulations applicable.
Mosaic safety controller cannot be used to control the actual burner as it requires analogical functions; nevertheless, Mosaic becomes an optimal solution to control the thermal process and plant safety functions as it’s able to handle a number of sensors required by the EN 746-2 standard, such as:
- Flame extinction monitoring: flame-presence detector sensors are normally used (often optical, non-safety) instead of the required SIL3-type or 2x SIL2-type flame detectors. More commonly, certified integrated burner monitoring systems (BMS), including flame control, are used. The SIL3-type or the 2x SIL2-type digital signal generated by the BMS can be used as input.
- Gas pressure monitoring: pressure switches (SIL2-type, SIL3 not available).
- Pilot-flame temperature control: temperature detectors (SIL3).
- Gas pipes purging control: gas detector (SIL3 or SIL2).
- Air-vent fans monitoring: flow sensors (SIL2).
- Air/fuel ratio monitoring: pressure switches (SIL2).
The block diagram shown below indicates the relationships between system’s components. The diagram clearly shows where Mosaic safety controller can take action. Based on the input received from sensors and safety systems, Mosaic OSSDs acts on the combustion-gas and combustive-air nozzles, controlling and adjusting the combustion process.
Process control (a)
- Control and instrumentation system / Operator control level
– Process control level
– Control level (local)
– Control (non-fail-safe)
– Tuning and adjustments
– Monitoring - Protective systems
– E-stop
– Safety interlock
– Purge and pipe monitoring
– Tightness control
– Automatic burner control unit
– Flue gas venting
– Air/fuel ratio
– Flow and pressure detectors
– High temperature limits
Heated system (b)
- Fuel supply (gas)
- Combustion air supply
- Burner system and ignition device
- Combustion chamber
- Processing chamber
- Flue gas system.
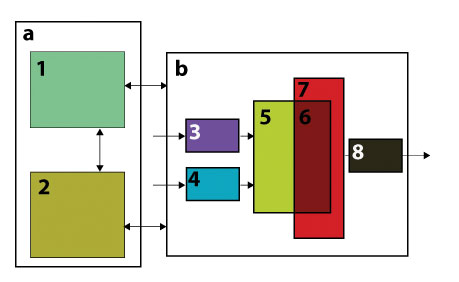
Standard
These types of systems are regulated by European Standard EN 746-2 – “Industrial thermoprocessing equipment safety requirements for combustion and fuel handling systems” May 2010.
This Type C standard, as defined by EN ISO 12100-1, is part of the 8 standards forming the EN 746 safety standards “Industrial Thermoprocessing Equipment”.
Note: The EN 746-2 assumes that all equipments are not creating any potential explosive atmosphere and are in a normally ventilated area.
EN 746-2 defines the requirements for the protective-and-safety systems of these devices:
- The protective-and-safety system is a group of devices, control units and safety circuits whose main purpose is the protection of the personnel, the plant and the environment.
- The protective-and-safety system includes all components required to carry out the safety function:
– Sensors for monitoring safety-related parameters (e.g. flame temperature, air pressure, etc..);
– Combustion-gas and combusive-air blocking devices (valves);
– Combustion-chamber ventilation control and burner protection devices (e.g. temperature level monitoring);
- A protective-and-safety system is typically made up of sensors, control logics, actuator devices and a multi-channel system allowing communication between all elements. The required safety monitoring of the whole system can be performed by Mosaic.
Mosaic Safety controller
Mosaic safety controller can be an optimal solution for the safety system of industrial thermal processes.
A typical safety plant for a traditional direct gas flame burner, controlled with one Mosaic master module (M1S), includes:
- 2 inputs for gas pressure switches – dual-channel redundancy.
- 2 inputs for flame detector sensors – normally used optical, non-safety sensor, instead of the required SIL3-type or 2x SIL2-type flame detectors.
- 2 input for air flow pressure switches – dual-channel redundancy.
- 1 OSSD pair for gas – dual-channel safety output to stop fuel supply.
- 1 OSSD pair for comburent (air) – supply fans control.
Note: Some plants may opt for different burners mounted in parallel. In this scenario, a main valve for common gas supply is usually in place. Nevertheless, the Mosaic configuration described above is still valid.
In more complex scenarios, or when Mosaic is used also to manage other non-safety functions of the plant, one ore more expansion modules could be required.
For more information,
www.reersafety.com