Leading Industry Associations Unite to Support Auto Components…
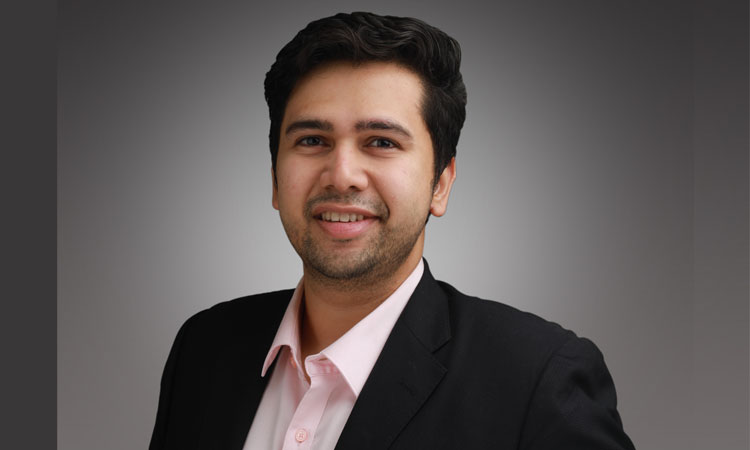
Combating Corrosion – The Jasmino Way | ENGINEERING REVIEW | Manufacturing | Industrial Sector Magazine & Portal | Indian Industrial Information | Manufacturing Industry Update | Manufacturing Technology Update
Founded in 1978 by Ramani Seshadri, an alumnus of the London School of Rubber, Jasmino Corporation began as a specialist in molded and extruded rubber products. In 1982, it ventured into rubber-based lining systems for corrosion protection, establishing a factory in Saki Naka, Mumbai. To offer integrated solutions, Jasmino Polymertech was later set up in Taloja, Maharashtra, combining equipment manufacturing and anti-corrosion linings under one roof. Over the years, Jasmino expanded its expertise to include a wide range of anti-corrosion linings and coatings, maintaining its expertise into rubber lining. With state-of-the-art equipment, facility upgrades, and certifications like ISO 9001, ASME “U” Stamp, and OSHA 14001, it became a trusted engineering partner in India. Adheesh Ramani, CEO, Jasmino Corporation speaks to Engineering Review and updates us on the company’s standing, wherewithal and growth strategies to take it to greater heights. Excerpts from the interview:
Adheesh Ramani, CEO, Jasmino Corporation Pvt. Ltd.
Q. Jasmino has come a long way from manufacturing rubber products to becoming a global player in anti-corrosive, wear-resistant solutions. Could you share some highlights from this journey and key moments that shaped the company’s growth?
Founded in 1978 by Ramani Seshadri, Jasmino Corporation began as a specialist in molded and extruded rubber products. In 1982, it ventured into rubber-based lining systems for corrosion protection, establishing a factory in Saki Naka, Mumbai. To offer integrated solutions, Jasmino Polymertech was later set up in Taloja, Maharashtra, combining equipment manufacturing and anti-corrosion linings under one roof. Over the years, Jasmino expanded its expertise to include a wide range of anti-corrosion linings and coatings, maintaining its expertise into rubber lining.
In 2018, Jasmino extended its global reach through collaborations with GBT Group Germany and Rubber Source USA, providing specialized lining solutions. With partnerships and vendor networks in Europe and the Middle East, Jasmino now operates across 15 countries including Jordan, UAE, Saudi Arabia, France, Poland, delivering turnkey solutions to industries such as petrochemicals, power, chemicals, fertilizers, and pharmaceuticals. Today, Jasmino is recognized for providing end-to-end engineering solutions, from design to manufacturing, ensuring world-class anti-corrosion protection and critical equipment manufacturing for industrial plants worldwide.
Q. Recently, Jasmino acquired two German companies, positioning itself as the third-largest company globally in corrosion protection. What strategic advantages do these acquisitions bring to Jasmino, and how do they align with the company’s long-term goals?
The recent acquisition of two German companies namely HAW Lining and Buecolit, marks a significant milestone for Jasmino Corporation, enhancing its ability to deliver high-quality, integrated solutions across a broader market. This move aligns with the company’s vision of becoming the global leader and preferred one-stop provider for critical equipment and protective lining systems in chemical-based industries, enhances Jasmino’s reach to both domestic and international customers. These acquisitions will not only boost revenue but also expand technological capabilities, and enhance its market share, further solidifying Jasmino’s leadership position.
HAW Lining, a 125-year-old pioneer and inventor of rubber lining, has been instrumental in protecting industries from corrosion worldwide. This acquisition grants Jasmino access to one of Europe’s largest equipment production facilities, covering over 120,000 square meters, including the world’s largest anti-corrosive lining shop floor.
GBT Buecolit, a leading German company in heavy-duty corrosion protection, specializes in coatings, plastic linings, and turnkey solutions. Operating across Europe with subsidiaries in Poland and the Netherlands and partners in Belgium, France, Switzerland, Luxembourg, and Jordan, GBT is renowned for its comprehensive engineering solutions. Its acquisition strengthens Jasmino’sEuropean presence, enhances its technical expertise, and boosts its ability to deliver efficient, reliable solutions while minimizing equipment downtime globally.
Q. Jasmino’s expertise in rubber lining plays a critical role in sustainable industrial operations. Could you elaborate on how this technology contributes to cleaner operations, especially for sectors like thermal power, petrochemical, and water treatment?
Rubber lining is a critical component in the chemical, petrochemical, fertilizer, and thermal power industries, playing a vital role in enhancing sustainability through its protective and functional properties. One of its primary functions is protecting equipment from corrosion. The harsh chemicals and environmental conditions in these industries can cause significant wear and tear on storage tanks and reactors. Rubber linings provide a seamless barrier that prevents corrosive substances from coming into direct contact with metal surfaces, shielding equipment from corrosion, high temperatures, and abrasive materials. This protection extends the lifespan of tanks and machinery, minimizing leaks, structural failures, and maintenance downtime while promoting a sustainable operational model.
Additionally, the durability and longevity of rubber linings reduce the need for frequent replacements, lowering overall material consumption and waste generation. This contributes to environmentally responsible practices by optimizing resource use and supporting sustainable industrial operations.
Q. With India’s thermal power plants mandated to install Flue Gas Desulfurization (FGD) units, what role does Jasmino play in this initiative? How does your technology help reduce sulfur emissions and align with India’s environmental targets?
Flue Gas Desulfurization (FGD) is a process used to remove sulfur dioxide (SO₂) from flue gas, which is the exhaust released during fossil fuel combustion. Sulfur dioxide emissions contribute significantly to air pollution and pose serious environmental and health risks, making FGD essential for thermal power plants. In India, approximately 260 thermal power plants are now required to install FGD units to clean their emissions before release, creating a market opportunity worth around INR 6,000 crore. Jasmino Corporation, with its advanced, indigenized technology for corrosion protection in FGD scrubbers, is well-positioned to capture a significant share of this market.
The key component of an FGD system is the Absorber or Scrubber, which uses wet limestone to react with and absorb sulfur oxides from raw gas after coal combustion. These Absorbers are exposed to highly corrosive and abrasive conditions, including acids, alkalis, and solid slurry particles, which can damage metal surfaces. To protect them, rubber linings are used as durable, corrosion- and abrasion-resistant barriers. These linings have an exceptional capacity to withstand sulfur dioxide, making them a long-term, cost-effective solution with a service life of 15 to 20 years, reducing maintenance costs, and improving the efficiency of power plant operations.
By reducing sulfur dioxide emissions, FGD systems significantly lower air pollution levels, helping India transition to cleaner energy practices. This aligns with the country’s goal of achieving its net-zero emissions target by 2070, as it reduces the environmental impact of existing thermal power plants and supports a gradual shift to sustainable energy sources.
Q. Jasmino has established a strong international presence in the Middle East and Europe. Are there any specific regions or markets the company is targeting next? What strategies are in place to drive growth in these areas?
Jasmino Corporation is strategically expanding its global footprint to tap into emerging opportunities in high-growth regions. In the Middle East, we are focusing on Saudi Arabia, which is diversifying its economy with significant investments in petrochemicals, mining and fertilizers sectors. Our partnership with the Al-Suhaimi Group and investment in a fully operational facility ensure a smooth entry into Saudi Arabia, while opening doors to neighbouring markets like Jordan, Kuwait, and Bahrain. With our expertise and regional alliances, we are poised to lead large-scale industrial projects in these sectors.
In Europe, rising manufacturing costs and a shortage of skilled labour creates an excellent opportunity for Jasmino to establish itself as a reliable and cost-effective solutions provider. Our acquisition of HAW and GBT has significantly enhanced our capabilities, enabling us to offer comprehensive turnkey solutions and strengthen our reputation as a trusted global partner. This expansion solidifies our position in Europe, aligning with our growth objectives and increasing our market share.
Additionally, we are exploring opportunities in Australia, particularly within the mining sector. Plans to open a dedicated office will allow us to serve this industrially vibrant market effectively.
Q. As Jasmino looks to the future, how do you see the demand for anti-corrosive and wear-resistant solutions evolving?
The demand for anti-corrosive and wear-resistant solutions, particularly rubber lining, is expected to rise as industries continue to expand and modernize. With initiatives like “Make in India” encouraging local manufacturing, there is an increasing need for critical equipment and lining materials that can withstand harsh chemical environments. Moreover, with major projects in the oil, gas, and petroleum sectors, the demand for new equipment, along with routine maintenance, will further drive the need for our solutions.
At the same time, industries are placing a greater emphasis on sustainability and eco-friendly practices. Rubber linings not only provide superior protection against corrosion but also help mitigate environmental risks, aligning with growing regulations that require businesses to adopt greener practices.Lastly, the maintenance sector will continue to be a key driver of demand. Rubber linings extend the lifespan of equipment by acting as a protective barrier against wear and corrosion, reducing the frequency of repairs and lowering long-term operational costs.
Q. With over 3,000 completed projects for prestigious clients like Adani Group and Reliance, are there any projects that stand out as particularly challenging or innovative?
One project we are especially proud of is a challenging assignment for BIFPCL Maitree in Bangladesh. This project was part of a commitment made by our Honourable Prime Minister to the Prime Minister of Bangladesh to commission a 2 x 660 MW power plant, a key component of the Friendship Treaty between India and Bangladesh.
Our role involved rubber lining two FGD absorbers with self-curing bromo butyl rubber. These absorbers are critical to the power plant, as the plant could not be commissioned without the rubber lining inside the FGDs.
The project came with significant challenges. The client had faced severe delays, and when the work was handed over to us, there was very little time left before the project inauguration, which was to be attended by Prime Minister Modi. This made it a high-stakes project of national importance, and our contribution was crucial to its success.
A project of this scale usually takes five months to complete. However, understanding the urgency, we quickly assembled a dedicated team of nearly 200 workers who worked tirelessly around the clock. We successfully completed the rubber lining of 6,350 square meters for the first absorber in just 25 days and finished the second absorber in only 20 days.
This achievement set a world record for the fastest rubber lining of such a large area, highlighting Jasmino Group’s ability to handle complex challenges and deliver high-quality solutions under tight deadlines.
Q. What new trends or technological advancements is Jasmino exploring to stay ahead in this field?
At Jasmino, we have always focused on research, development, and innovation. Over the years, we have developed strong in-house expertise, allowing us to create customized solutions for our customers. By understanding their specific needs, we often design rubber formulations tailored to their chemical processes.
Recently, a client faced major challenges at their plant and approached us for help. We developed a new rubber lining system using bromobutyl rubber that could handle continuous operations at temperatures up to 135 degrees and temperature shocks up to 155 degrees. While standard bromobutyl systems are typically rated for 100 degrees, our dedication to rubber R&D allowed us to create a solution that perfectly matched their requirements.