The Next Frontier In Industrial Safety: How Low-Voltage…
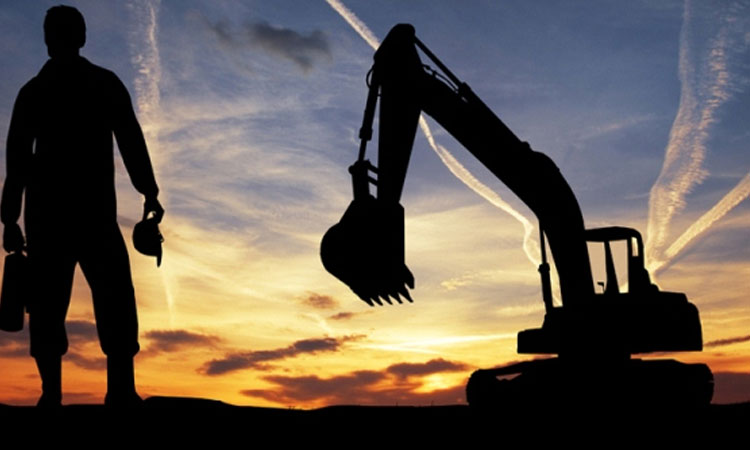
A simulation approach for autonomous heavy equipment safety | ENGINEERING REVIEW |Manufacturing | Industrial Sector Magazine & Portal
The heavy equipment customer’s main objective is to increase their machine efficiency in the field by producing more with less while keeping a strict eye on operator safety. But with machines that become more and more specific, more and more complex, guaranteeing people safety and machine integrity also depends a lot on the operator’s skills.
Partly or fully automated machine operation is a solution that most of the industry stakeholders are already investigating to increase safety and improve operability. Consequently, they can lead the digital revolution we face today.
With an increasing number of Advanced Driver Assistance Systems (ADAS) features to improve operator safety, such as remote-control driving/actuation or fully autonomous driving, the interactions between the operator and the vehicle are being reshaped. Nevertheless, working on heavy equipment autonomous operations means partially or fully replacing a skilled operator. These operators bring four main elements to their position: his/her senses, his/her brain, his/her experience, and the environment they interact with.
The role of simulation and of the digital twin
Model-based systems engineering (MBSE) is an approach that fits perfectly with the development of autonomous vehicles – many companies have been using it for years. Today, we’ve entered a period of intense innovation, and manufacturers are under tremendous pressure to reduce program costs. We see more system autonomy to deliver new mission capabilities leading to more interactions between the thousands of systems, interfaces, and components on a single heavy machine.
When it comes to product design and performance engineering, the MBSE approach brings the so-called ‘Digital Twin’ of the product/vehicle as well as its environment. It allows engineers to virtually explore the autonomous vehicle designs, as well as accelerate advanced control verification and validation, which can be tough for vehicle durability and expensive if pursued using a classical physical testing approach. Even if you work with the state-of-the-art data acquisition solution dedicated to ADAS.
Autonomous heavy equipment natural environment simulation
When it comes to the natural environment modeling, the simulation solution should be open and flexible enough to allow the import of any type of:
- off-road vehicle geometric models,
- geometric terrain with a relevant drop, slopes, and obstacles like rocks, trees, pedestrians, other vehicles,
- harsh conditions implied by the natural environment seasonality (rain, fog, dirt, day & night, sunset or sunrise, etc.)
This allows to perfectly match with conditions regularly encountered by heavy-equipment vehicles.
To create a good virtual digital twin of the field environment, Simcenter Prescan, the solution developed by Siemens Digital Industries Software (DISW), ensures objects have a good enough geometric description and material property description by considering what is important for each sensor modality: camera, LiDAR, radar.
Additionally, Siemens DISW teams have been working in the past years on the coupling between its environment and its system simulation software, as well as investing in improved ground modeling technology. The Simcenter Amesim Track generator feature is an example. This feature allows the implementation of bumpy soil, with a certain penetration coefficient to consider the impact of the soil on autonomy sensor performance at vehicle low or high speed. The interactions between vehicle dynamics, traction on soft soil, and the powertrain are crucial.

Any relevant obstacles associated with the scenarios of interest can be implemented as part of the environment. The objective is to analyze the sensor’s detection and object recognition algorithm performances. Rocks, trees, buildings, crops, pedestrians, wildlife, infrastructures, etc. are elements that are relevant for our autonomous heavy equipment simulation environment, adding object motion when necessary.
Physical sensor modeling
When it comes to the replacement of the operator senses, one question summarizes the engineering challenges of implementing sensors like cameras, radars, LiDARs: How can you predict what the machine will or will not sense?
Consider that a physical sensor modeling solution is mandatory for a simulation platform dedicated to autonomous operations development. Indeed, optimization of the sensor design and their configuration can be done virtually to a large extent.
From basic ground truth sensors (that identify all objects that appear in the sensor range), through probabilistic sensor models (that allow for fault insertion and filtering), up to physics-based sensor models (for raw data simulation), we can support engineers with balancing accuracy and computational time of sensors simulations based on mission/scenario requirements, for an improved engineering workflow efficiency. To have a robust sensor simulation, it is important to take into consideration three key components
- The physical sensor device,
- The world,
- The simulation engine.
The simulation engine is what brings together the physical device and the world. It allows us to handle important effects based on real-life physical equations. For example, for the radar and the LiDAR simulation, an in-house ray-tracing framework accurately captures how light or a beam is propagated through a scene got developed in Simcenter Prescan. We believe that having a high accuracy simulation engine is important to ensure that developers, testers, integrators, and authorities can trust Siemens as a key partner.

On top of the sensor modeling, engineering departments can use simulation to optimize the machine design itself for better sensor performances. For example, to prevent sensor soiling or too much electric/electromagnetic disturbance from a metallic bumper covered by mud or rain, both of which. impact heavy equipment vehicles daily and yet not considered enough in current solution portfolios.

Heavy equipment vehicle modeling
A skilled operator has hours of machine operations background experience. In order to improve the performance of the autonomous operations of the vehicle, it is mandatory to include accurate dynamics within the control virtual training, verification, and validation process. From soil and tire model to the vehicle dynamics, the more physics you implement the more robust your control will be, improving operability and safety.
The automation of the machine positively impacts other attributes. Indeed, it enables to better control the energy distribution, or yet powertrain actuation resulting in improved powertrain durability, keeping the machine within the safety zone of loads.
Simcenter simulation platforms, like Simcenter Amesim system simulation software and Simcenter 3D Motion, propose a large heavy equipment vehicle modeling capability: from construction equipment, transportation, agriculture, to military intervention autonomous robots, including the relevant vehicle and powertrain dynamics for each application. Simcenter Amesim, for example, can connect to the natural environment model using smart co-simulation FMI/FMU technology as has been shown in the previous video of the autonomous tractor in the cornfield. Engineers can thus consider the realistic vehicle dynamics impact on sensor and algorithm performances along the development workflow.
The machine type does not limit itself to the ground vehicles. Siemens DISW also proposes the integration of autonomous drones, including flight dynamics. That capability is usually used for terrain recognition, crop identification, and supporting to autonomous vehicle decision strategy.
Automate and accelerate the verification workflow
A key element leading to a significant reduction of the cost of autonomous heavy equipment simulation is the automation of the algorithm verification and validation workflow. Indeed, automating the validation of algorithms performance under various weather or lighting conditions, or simply making sure that the workflow covers all possible scenarios, allows an improved coverage of your perception algorithm validation, not talking about development time and cost-saving associated with this automation.

Sensor and vehicle configuration, sensor mounting, and vehicle design exploration can also be automated. In the example above, Simcenter HEED, Siemens DISW design space exploration, and optimization software package allow this performance verification automation.
The objective is the deployment of the virtual verification framework of ADAS and autonomous vehicle systems, allowing easy scenario generation, efficient critical case identification, and systematic virtual verification of requirements. In other words, automate and accelerate the scenario set-up, the interaction between the different simulations, and the post-processing of relevant metrics, for a quick and efficient Key Performance Indicators (KPIs) analysis.