Sugatsune introduces Swivel Torque Hinge HG-S for smooth…

Passion for Quality is in our DNA: Sreeramachandra Murthy, LMW | Engineering Review
Lakshmi Machine Works Ltd., popularly known as LMW, is a dominant name in the machine tool scene. The Machine Tool Division of LMW started in 1988 in collaboration with Mori Seiki of Japan, today makes a comprehensive range of CNC turning centres, machining centres, turn-mill centres and machine subsystems like tool-posts and a variety of spindles for the domestic and overseas markets. It makes 3,200 machines a year. The entire machining shop is supported with AHUs with positive pressure system. All castings for building machines come from LMW’s own foundry. The company has a wide array of precision production machines which are the world’s best brands. The assembly cell is fully temperature controlled. And every component going into the machines is tested for process capability. Today LMW is exporting its products to 23 countries across the globe, explains K. Sreeramachandra Murthy, President, LMW – Machine Tool Division in an interview with Machine Tools World. Excerpts:
Q. LMW is popular for textile machinery. What’s your standing in this domain?
LMW divisions are involved in manufacturing machines and products for various sectors namely the textile spinning, machine tools, precision castings and aerospace components and sub-assemblies. LMW started with the textile machinery division and is over five decades old now. We are among the top three in the world, manufacturing the entire range of spinning machinery. The company plays a very important role in the global textile market and is the leader in India with an enviable market share. The customers see great value in our products.
Q. When was the Machine Tool Division started? Could you narrate its growth story?
The machine tool division was started in 1988 in collaboration with Mori Seiki of Japan. This was with a vision to bring the best-in-class machines for manufacturing at a time when the component manufacturing was in a nascent stage – a time when the auto industry had just started introducing new generation vehicles in all segments, be it the 2-wheeler, 4- wheeler, LCV & HCV’s in the Indian market. The appliance manufacturing also saw a surge in this period and a greater need for higher quality parts.
We could address the parts quality demand with our machines, and we provided the much needed import substitution. The Indian manufacturing segment could produce world- class machines that were priced moderately which benefited the customers by saving precious foreign exchange by not importing machines.
LMW textile machinery division by 1988 was already one of the largest CNC machine users and was importing most of the machines. The machine tool division also catered to textile division’s captive requirements. LMW pioneered in high quality machines and became the benchmark for capital goods manufacturers. We started with just a few machines in the first year of operation and now we make over 3000 machines a year.
Q. What’s your present range of manufacture?
We primarily offer three types of machines viz. the CNC Turning centres, Machining centres & Turn-Mill centres. All machines are offered either as stand-alone machines or as turnkey and customised solutions. This includes automation and measuring systems. Our machines are also IOT ready. The machine tool division started with three models and now we have over 55 models with about 88 variants.
Q. What’s special about your CNC turning centres?
It’s not just the turning centres but our entire range of machines & solutions.
Well I would say that the speciality comes from the design, process of manufacturing and stringent quality control norms. The passion for quality is in the DNA of the company since its inception, we have also invested in the best-in-class mother machines and use state-of-the- art measuring equipment, The employees take great pride in being the quality leader and with it comes a high degree of passion. The performance feedback of the machines and repeat business from our customers are testimony to the machines being special.
Q. What are the unique features of your machining centres?
The machines are designed to be very robust. We extensively use CAD features to simulate the conditions. This helps in getting very close to the desired results even at the prototype stage, and having our own top-class foundry helps us in having an extremely good base structure.
In every machine manufactured, we try and maintain tolerances much lesser than the permissible limits as per international standards. Achieving this requires great attention to detail. I can also proudly say we make the best spindles for machining centres. The very fact that our machines are used in many high precision applications speaks volumes for the quality of our products.
Q. What are the integrated solutions you offer for the die & mould industry?
The Die & Mould industry requires very rigid & precise machines and our build quality takes care of this requirement. A Thermally stable machine in dynamic conditions is also a very important factor for this Industry. This is taken care at the design stage itself and the quality of base casting adds to the performance of the machine.
We offer a host of spindle speed ranges to meet various requirements, glass scales for higher precision, various types of spindle cooling mechanisms & measurement systems.
We have a strong application department who offer customized solutions, be it programming, tool selection, fixture design and manufacturing or as a complete turnkey solution. This is backed by a network of highly trained service engineers who are present nationwide. So when you buy an LMW machine, the support comes along with the machine and the customer doesn’t have to look beyond us to meet his requirements. That’s what we mean by ‘Integrated solutions’.
Q. What are the critical machining solutions you offer to the aerospace industry?
Aerospace sectors often utilize materials that demand special considerations such as Titanium, Special Alloy, Inconel and Special Composites, etc. Aerospace Segment requires high precision components to be machined. In order to achieve this accuracy and precision machining, we supply machines with customized solutions, specialized fixtures and special toolings. We also have our own division catering to Aerospace, Defence and Space requirements. Most of the machines used here are our own machines, This gives us better insights to the requirements of this sector and we tune the machines accordingly. There are customers who use our machines for some engine parts, valves & nozzles. The precision class of these components is very high and we have been able to take up this challenge and help manufacture these components.
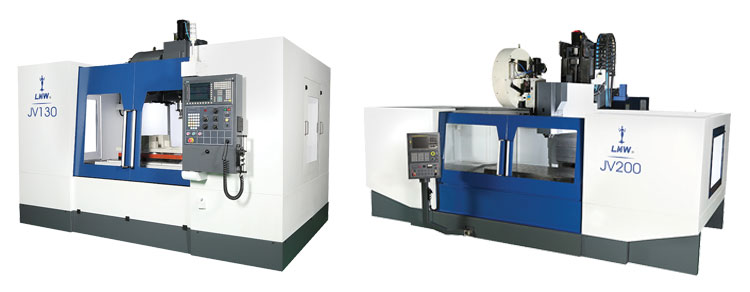
Q. What are the technological innovations you have showcased recently?
We have recently introduced a 5-Axis simultaneous machining center named the JU60. This was developed as a precision class machine for the aerospace industry. This machine is designed to have complete thermal stability and this ensures that the complex profile parts made on this are consistent with very low rejections. The machine is also capable of producing complex Dies which also need very high surface finish. The machine is designed in such a way that we can easily adapt and configure to meet different requirements.
Q. You have a tie-up with DMG Mori for manufacturing machines for their Indian customers. What’s your success rate in making machines to DMG Mori design and specs? How many machines have you supplied in the last one year?
Yes, we make machines for DMG Mori. They are of the same standards as a machine made in Japan or Germany. The machines cater to the world market and not only for the domestic segment. We have supplied significant number of machines and all the customers are satisfied with the build quality and performance.
Q. Could you update us on your manufacturing facilities, capabilities and excellence?
This plant was started in 1988 and was one of the most modern plants at that time. We have been constantly upgrading our facilities with the best available mother machines and state-of-the-art measuring equipment. The plant is dust-free and the assembly line is air conditioned to maintain high quality levels.
Q. How do you instil quality in your products?
A clean and temperature-controlled atmosphere is dedicated for critical assembly to ensure total quality control. We have a wide range of advanced equipment and methods to ensure maximum accuracy and precision machine assembly. Our quality assurance has all the latest systems and instruments for testing and inspection. Every machine manufactured undergoes a set of mandatory tests. This is time-consuming as well as expensive. However this is the only way we can ensure defect-free products are delivered to customers.
Q. Could you throw some light on your target markets and global presence?
We have a very strong presence in the Auto sector. Our presence is growing rapidly in other sectors as well like the Die & Mold, Oil & Gas, Medical, Aerospace, etc.
Our capacities are mostly occupied meeting the domestic demand. However, we have presence in Russia, Vietnam, Bangladesh, China, United Arab Emirates (UAE), Saudi Arabia & Kenya. We envisage increasing our presence in South Eastern countries at this point of time.
Q. What are the safety measures you take in the wake of Covid-19 and what are the challenges ahead for you in the new normal?
Well, this has been a challenge. Some of the measures we have taken are:
- Screening of employees and visitors for body temperature and sanitizing hands and footwear is mandatory
- Sanitizers are kept at convenient locations for use by employees
- Encourage workers to stay home if they are sick & allow work from home wherever possible.
- Wearing Masks is mandatory
- Encourage Virtual meetings
- Non-contact attendance system instead of biometric systems
As a change of strategy we had to accelerate the customer-connect programs through webinars, tele-calling & social media (Virtual Exhibitions) for various industrial segments. The Covid effect was seen only for three months. Thereafter there was a surge in consumption driven by all segments including auto components. To cope up with the demand, safe travel of field staff had to resume with extra precautions and avoiding any public transport.
The key addressable issues continue to be productivity, effectiveness, cost-competitiveness and customer experience across users. At the same time, employees’ safety and safe working conditions are of high priority.