Hitachi Strengthening its Analytical Business to Solve Social…
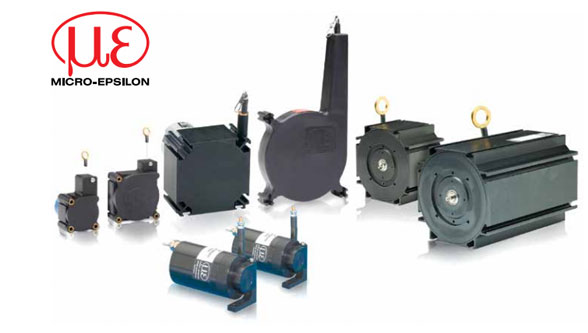
Draw-wire displacement sensors for mobile automation
Draw-wire displacement measurement sensors have been available on the market for more than 60 years. These sensors are widely used in displacement measurement technology.
The proven wire SENSOR family of draw-wire sensors is available in many different sizes, shapes and variants. The measuring ranges are individually selectable between 50 and 50,000mm in many different graduations. The special feature here is the compactness of the sensor for its respective measuring range. For example, the diameter of the smallest version of the sensor is just 30mm with a measuring range of 750mm. Many different analogue and digital outputs are available, as well as housings made from plastic or aluminium. As only high precision components are used in its design, the sensors benefit from a longer than average service life. Wherever distances and tilt angles need to be measured by contact, draw-wire sensors are ideal.
Positioning of catering vehicles for the Airbus A380
Catering trucks are an important supply medium for modern airliners. They are used for loading and unloading an aircraft with food. Based on a hydraulic scissor-type mechanism, the van body of the truck is raised until the best position to access the supply door is reached.The company Doll from Oppenau produces these catering vehicles. As one of the handful of suppliers, they are able to safely supply an Airbus A380 whose supply door could be located at a height of more than 8m.The catering truck cannot drive directly to the supply door, because this door is above the wing, not beside it. Therefore, the complete van body is moveable in a longitudinal direction.A further challenge on the design is the ambient temperature range of -25°C to +65°C.The corresponding change in the oil viscosity also causes changes in the speed of the positioning hydraulics.Therefore, to dock safely and reliably to the aircraft, the movement of the van body must be detected by using a measurement system.
WDS-xx-P115 series draw-wire sensors from Micro-Epsilon are used for this. Mounted between the van body and the scissors system, movement is measured precisely and reliably.The extreme ruggedness and long service life convinced Doll to integrate the sensors. They provide precise measurement results, high reliability against failure, even in poor weather conditions and optimise the set up and removal time of the catering vehicles.
Lift-height measurement in forklift trucks
Logistics is critical today and will be even more important in the future. Increasing supply chains of goods must be shipped and transferred in ever-shorter time periods. As a result, logistics service providers are attempting to shorten the transfer times in the warehouse and to optimise warehouse movements.Here, a high level of potential optimisation can be exploited by applying displacement sensors in forklift trucks. Typically when raising and lowering the load, large safety margins must be observed, so that when rounding a corner, or braking and accelerating suddenly, the truck is not placed in a dangerous tilted position.
If the lift height of the load can be measured, the optimum driving speed can be determined from this. In addition, the system is protected against misuse or manual errors i.e. the operator cannot knowingly or unintentionally cause unsafe driving conditions.
This then optimises the speed but also improves the safety of the operator.Furthermore, the sensor can also be used to automatically bring the load to the correct lift height in order to speed up the movement to the correct shelf height.It is specially adapted to the requirements of the forklift truck. For safety reasons, the sensor is designed redundantly. Two electrically independent signals ensure that a high level of safety is achieved.
Lift height measurement for two-column lifts
Modern two-post lifting systems are normally designed without a base frame.Unlike conventional lifts that have a chain between the two lifting columns, this means that modern systems require no mechanical connection. Therefore, the typical normal threshold between the lift columns is no longer required.This makes the user’s daily work much easier.No “obstacle” has to be overcome during entry and exit and so it is much easier to position the vehicle.
However, “automatic” lift height synchronisation, which was previously provided by the mechanical connection of the two columns, is now missing.The lift therefore requires a synchronisation controller or lift height monitoring system in order to ensure that the vehicle is raised evenly on both sides.Draw-wire sensors are the preferred choice for this type of height measurement.
These sensors are easy to integrate, very compact and provide a very attractive price / performance ratio relative to the measuring range, as well as high accuracy.Depending on the measuring range and required protection class, the P60, P96 or MK77 series are ideally suited to this application.There are many different output signals available, which means the sensors can be easily adapted to the respective controller. Also analogue signals (voltage, current, resistance), incremental (HTL, TTL) or absolute (CANopen, Profibus, SSI) digital outputs are also possible.
Choosing a suitable sensor for the respective application is also based on the combination of the individual key features. It is the long measuring range and the opportunity to output two electrically redundant signals that makes all the difference when it comes to measuring the height of a fork-lift truck.Another important factor: while high reliability and a low failure rate is normally associated with mechanical components, these qualities can only be achieved cost- effectively using electronic components by using redundant structures. For a draw-wire, this opens up the possibility, mechanically speaking, of designing a sensor with two sensor elements (e.g. potentiometers) and therefore cutting the cost compared to other technologies. A changeover from switching systems to continuously measuring ones leads to material savings and time, while ultimately increasing the efficiency of the final product. For example, when the lift height of a forklift truck is monitored, the traverse speed is continuously adjusted to the level of the load, which leads to improvements in throughput efficiency.Consequently, Micro-Epsilon has the largest product portfolio available on the market.The main role is not played by the high technical performance in terms of resolution or speed. Instead, it is on a comprehensive package based on technical requirements, durability and price.A large choice of catalogue products combined with years of experience in small series, enable the sensors to be easily adapted to specific customer requirements and a cost-effective sensor solution to be provided.