The Next Frontier In Industrial Safety: How Low-Voltage…
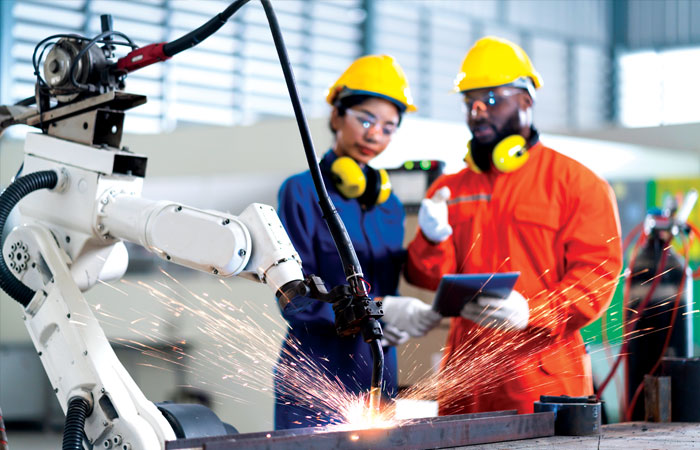
Automation In The Welding Industry – New Trends | ENGINEERING REVIEW | Manufacturing | Industrial Sector Magazine & Portal | Indian Industrial Information | Manufacturing Industry Update | Manufacturing Technology Update
The Fourth Industrial Revolution (Industry 4.0) is the trend towards automation and data exchange in manufacturing industry technologies and processes, including cyber-physical systems (CPS), IoT, the industrial internet of things, cloud computing cognitive computing, and artificial intelligence.
Industry 4.0 also impacts the welding industry, from the increased use of automation and robotics to data analytics that improves future welds. AI and new welding technologies are also enabling new possibilities in industries that utilize the latest and most delicate metals that require the highest level of control during welding. As the industry continues to evolve, we expect to see further advancements in welding that will enhance safety, improve quality, and increase productivity.
Robotic Welding
Over the years, robotic welding has been utilized in various industries to increase productivity by automating production and ensuring consistent quality. Traditionally, robotic welders required significant investments in equipment and personnel training. However, they have evolved, so today, they offer a unique set of advantages, such as:
- Production automation
- Overall cost reduction (high initial cost, but they pay off as they increase productivity)
- Consistency and repeatability lead to increased quality and accurate welds
- Personnel are not exposed to hazardous fumes or radiation
- Deals with high demand for a skilled workforce by utilizing operators, not welders
- Increased flexibility (versus hard automation)
- Efficiency improvements (useful in mass production)
- Reduce repetitive strain injuries
Welding Cobots
Besides robots, the manufacturing process utilizes cobots. A welding cobot, or collaborative welding robot, is designed to assist human welders in the welding process. It is equipped with sensors and programming that allow it to work alongside human welders without the need for safety barriers or cages.
The welding cobot can perform various welding tasks, and it is programmed to work collaboratively with human welders, assisting them with the more repetitive or physically demanding aspects of welding. One of the main advantages of welding cobots is their ability to improve the safety and ergonomics of the welding process. For example, advanced welding equipment and sensors make the cobot aware of welders and operators nearby, so it stops to prevent collision and hurting the operator. Meanwhile, robotic welding machines are pre-programmed, so they can severely hurt you if you get in their way.
Welding Drones
Welding drones are crewless aerial vehicles (UAVs) equipped with cameras, sensors, and robotic arms to perform welding tasks and inspections. Drones are instrumental in hard-to-reach or hazardous locations, such as high-rise buildings, bridges, or offshore oil platforms, which present the riskiest environment for any welder.
The drones are remotely operated by a human operator who can monitor the welding process and make adjustments as necessary. In addition, they can access and weld in hard-to-reach locations, which can save time and money by eliminating the need for scaffolding or other access equipment.
Additionally, welding drones can perform welding tasks in hazardous locations, reducing the risk of injury or death to human welders. This makes welding drones particularly useful in industries such as oil and gas, where welding tasks are often performed in dangerous or remote locations.